The mission is intended to help determine the origin and distribution of the moon's water and whether enough could be harvested from the moon's surface to support people living there.
While the prototype wheel printed at DOE's Manufacturing Demonstration Facility, or MDF, at ORNL will not actually be used on the NASA Moon mission, it was created to meet the same design specifications as the wheels made for NASA's VIPER. Additional testing is planned to validate the design and fabrication method before using this technology for future lunar or Mars rovers or considering it for other space applications, such as large structural components.
Additive manufacturing can reduce energy use, material waste and lead time, while enabling design complexity and the tailoring of material properties. MDF is at the forefront of this effort, developing the technology for over a decade for a wide range of applications in the clean energy, transportation and manufacturing sectors. MDF researchers printed the rover wheel prototype at ORNL in Fall 2022. A specialized 3D printer used two coordinated lasers and a rotating build plate to selectively melt metal powder into the designed shape.
Typical metal powder bed systems operate in steps: In a machine the size of a cabinet, they rake a layer of powder over a stationary plate. Then a laser selectively melts a layer before the plate lowers slightly and the process repeats. The printer used for the rover wheel prototype is large enough for a person to enter and is unique in its ability to print large objects while the steps occur simultaneously and continuously, said Peter Wang, who leads MDF development of new laser powder bed fusion systems.
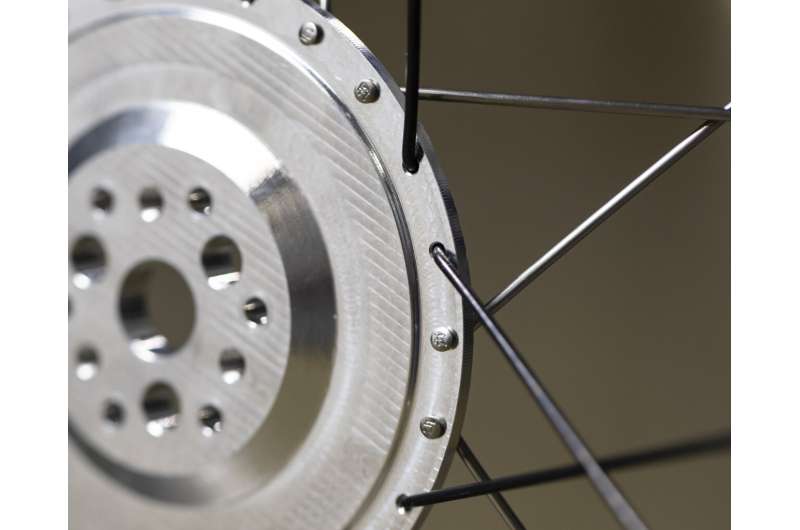
"This dramatically increases the production rate with the same amount of laser power," he said, adding that deposition occurs 50% faster. "We're only scratching the surface of what the system can do. I really think this is going to be the future of laser powder bed printing, especially at large scale and in mass production."
Wang and project team members recently published a study, published in 3D Printing and Additive Manufacturing, analyzing the scalability of the technology for printing components like electric motors.
Although the machine is unique, a key to the success of the project was researchers' expertise in process automation and machine control. They used software developed at ORNL to "slice" the wheel design into vertical layers, then balance the workload between the two lasers to print evenly, achieving a high production rate, leveraging a computational technique recently submitted for patent protection.
The prototype wheel, one of the first parts produced by the system, demonstrates the value of interagency collaboration. "The project with NASA really propelled the technology forward," said Brian Gibson, the researcher who led the rover wheel project for ORNL, calling it a milestone. "It was great to connect a capability with a developing need, and the team was excited to be making a prototype component with space exploration applications."
Made of a nickel-based alloy, the prototype wheel is about 8 inches wide and 20 inches in diameter—much larger than typical parts printed with metal powder bed systems. Making it required the ability to print small geometric features spread over a large work area. Additive manufacturing enabled greater complexity in the rim design without added cost or manufacturing difficulty, Gibson said.
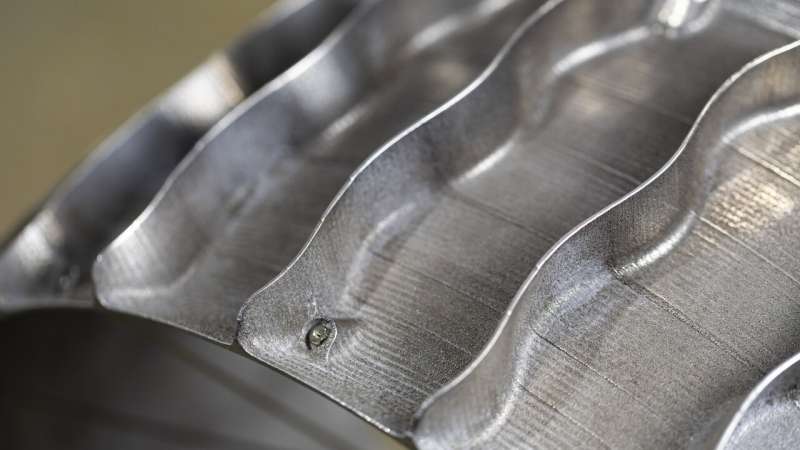
In comparison, the four VIPER wheels that will churn through moon dust next year required multiple manufacturing processes and assembly steps. VIPER's 50-piece wheel rim is held together with 360 riveted joints. The manufacturing process required complicated and time-intensive machining in order to meet the mission's rigorous requirements.
If NASA testing proves the 3D-printed prototype to be as robust as conventionally built wheels, future rovers could instead use a single printed wheel rim, which took ORNL 40 hours to manufacture. Through the project, ORNL and NASA engineers also explored printing precise design features, such as angled sidewalls, a domed shape and wavy tread to increase the wheel's stiffness.
These characteristics are difficult to incorporate in the current VIPER wheel design using traditional fabrication methods. Despite enabling a more complex spoke pattern and spoke locking features to the wheel, 3D printing simplified and reduced the cost of the wheel design and made final assembly easier.
"A lot of these wheel features were put in just to highlight what you can do with additive manufacturing," said Richard Hagen, a mechanical design engineer for NASA and additive manufacturing lab manager at NASA's Johnson Space Center in Houston. "It lets you easily implement design features that are hard to implement with traditional tooling or even a traditionally machined part." ORNL's ability to print large objects demonstrates the potential of additive manufacturing technology for producing much larger rover wheels for both lunar and Martian missions, Hagen said.
A challenge is that the specialized printer only builds with certain materials—in this case, a nickel-based alloy—so the 3D-printed wheel is 50% heavier than the aluminum VIPER wheel, while printed at a similar thickness.
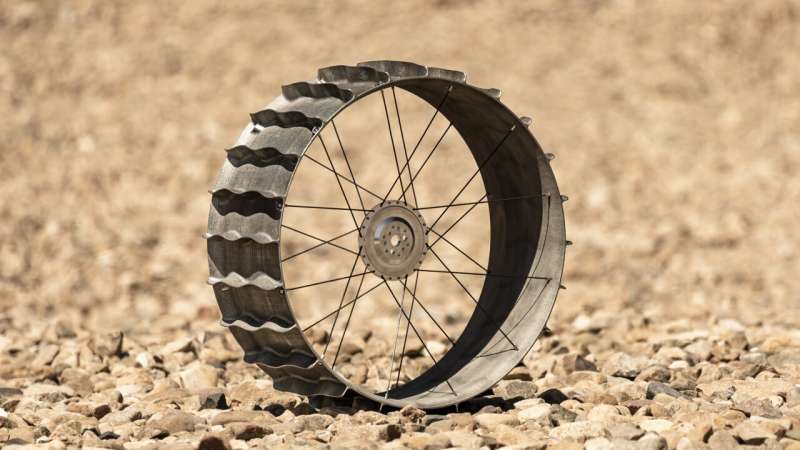
NASA plans to test the 3D-printed wheel's performance on a rover either in the rock yard at NASA's Johnson Space Center or in a giant "sandbox" of simulated lunar rocks and soil at a contracted test facility. Evaluators will assess the wheel's maneuverability, pivoting resistance, sideways slippage, slope climbing and other performance metrics.
Hagen said additive manufacturing offers the advantage of rapid design updates in response to testing. It can also incorporate more complexity, such as a suspension system, without adding weak points.
Hagen said crewed research stations placed on the moon as part of the agency's Artemis Program will need off-planet manufacturing capability. "Being able to build parts in space for repairs will be important, because you just can't take enough spares," he said. "Powder, pellets or filament for printing are a lot easier to pack and would allow for more flexibility."
"Additive manufacturing offers the flexibility that if you have the feedstock, you could make any replacement part you need, whether in space or on Earth," Gibson said. This is a reason additive manufacturing has generated significant interest for a range of replacement needs, from rapidly manufactured tooling to hard-to-source castings and forgings. For space exploration and habitation, 3D printers could eventually use local material from the moon or Mars as a feedstock.
More information: Peter Wang et al, Improved Productivity with Multilaser Rotary Powder Bed Fusion Additive Manufacturing, 3D Printing and Additive Manufacturing (2023). DOI: 10.1089/3dp.2022.0288
Provided by Oak Ridge National Laboratory