A recent paper titled "Robots Made From Ice: An Analysis of Manufacturing Techniques" explored that possibility. The paper was presented at the 2020 IEEE (Institute for Electrical and Electronics Engineers) International Conference on Robotics and Systems. Devin Carroll and Mark Yim wrote it. Carroll is a Ph.D. robotics student at the University of Pennsylvania, and Yim is the Director of the Grasp Lab and a professor of mechanical engineering at the same institution.
The entire robot wouldn't be made of ice, obviously. But some of the structure could be. The idea is centered around a modular design that could self-repair or even self-replicate and could be completed in-situ after deployment, once terrain obstacles and the details of the mission's tasks were better understood.
In their abstract, the two authors write, "The ice allows for increased flexibility in the system design, enabling the robotic structure to be designed and built post-deployment after tasks and terrain obstacles have been better identified and analyzed."
Obviously, there are a lot of problems and obstacles with this potential technology. But that's how they all begin.
The pair of authors make it clear that this is preliminary work. "The authors explore a structure-driven approach to examine compatible manufacturing processes with an emphasis on conserving process energies," they write. "A mobile robotic platform made from ice is presented as a proof of concept and first demonstration."
The idea is centered on a two-wheeled rover named Icebot. Icebot is based on the design for Antarctic rovers and has structural elements made of ice.
In their work, the pair of authors performed experiments to explore the whole idea. The work was based on two assumptions:
- The robot will be operating in sub-zero temperatures, and all of their calculations are based on average yearly temperatures at McMurdo station in Antarctica.
- Blocks of ice are readily available.
Their paper also presents three general design principles.
- Components need to be designed to manage heat.
- All electronics, actuators and power sources must be isolated from melting.
- The ideal method to shape the ice components of the robot depends on the final volume of the part relative to the volume that must be removed from a raw slab of ice.
There's another overarching condition in all of this, too. For robots operating on other worlds, energy is a precious commodity. Each mission has an energy budget that is meticulously managed. Take the Voyager spacecraft, for example. Their impressive longevity is due at least in part to extremely scrupulous use of energy. So the amount of energy an ice robot uses to manufacture and build itself is critical.
With those conditions in mind, the researchers came up with some interesting ideas.
First of all, the entire scenario would likely involve not a single robot but a pair, operating in tandem. One unit would be the primary exploration vehicle, and the other would be kind of like a mother ship and would have the manufacturing and repair capabilities.
In an interview with the IEEE Spectrum, Devin Carroll explained what this might look like. "When I think of an arctic (or planetary) exploration robot that incorporates self-modification or repair capabilities I envision a system with two types of robots—the first explores the environment and collects materials needed to perform self-augmentation or repair, and the second is some sort of manipulator/manufacturing system. We can envision the exploration class of robot returning to a centralized location with a request for a plow or some other augmentation and the manufacturing system will be able to attach the augmentation directly to the robot."
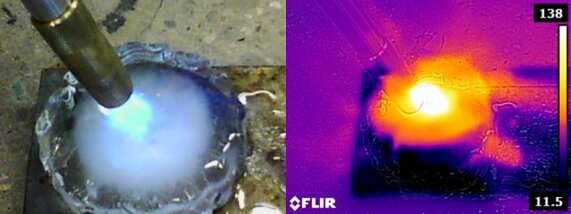
The pair of scientists performed some tests to flesh out their ideas. They looked at different ways of manipulating ice. For manufacturing, they looked at molding, where ice would first be melted then poured into a mold to be shaped. They also looked at 3-D printing, and machining. Each method has its pros and cons, and each one has different energy requirements.
They also looked at actuator integration. As explained, actuators themselves can't be made of ice. Actuators are exposed to different stresses, ice can't handle it. So the integration of the actuators with components made of ice is a critical operation.
They experimented with four different ways of integrating actuators:
- Mechanical carving with something like a chisel.
- Melting a hole for the actuator with open flame.
- Creating a hole for the actuator with a heated metal rod.
- Cutting, for example, with a hole saw.
Each of the methods has their strengths and weaknesses. Each one also has its own energy requirements. The table below presents the energy required for each method to create a mounting pocket for the actuator, and to freeze it into place.
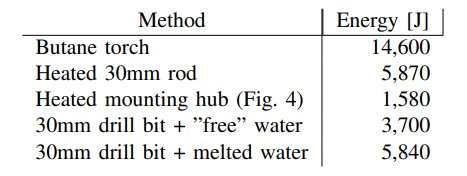
Since this is preliminary work, the team didn't reach any permanent conclusions. But their experiments exposed some pitfalls that will need to be overcome if in-situ ice manufacturing and repair is ever going to be implemented effectively.
They found that the surface area of the attachment is critical for success, which isn't a surprise. In a nutshell, a larger surface area in the joint is better, and helps the ice resist stresses due to torque and other forces. Ice thickness was also an issue, which is also not surprising.
The authors sum up their work in the paper's conclusion. "This work is a step toward a lightweight, adaptable robotic system capable of operation in subzero environments. This system lends itself to self-reconfiguration, self-replication and self-repair," they write.
"To push toward the development of automated methods for creation and assembly of this system we plan to pursue a joint module that can be easily integrated with passive blocks of ice," they write. That would make the IceBot system simpler and more modular.
They also explained what the future holds for their IceBot concept: "Additional future work includes: determining a general class of surface on which this system can move, methods of using ice elements to interact with the environment, and further investigation into the strength limits of the connections between actuators and the ice."
In the Spectrum IEEE interview, Carroll also talked about what's next for their IceBot efforts and emphasized the need for modularity. "My immediate focus is on designing a modular joint we can use to easily and securely join actuators with blocks of ice as well as working to develop an end effector that will allow us to manipulate blocks of ice without permanently deforming them via screw holes or other, similar connection methods."
There's a lot of work to be done before any ice robotics technology can be implemented. But it's a tantalizing development, and Europa and Enceladus are waiting. Agencies like NASA are taking a close look at in-situ resources for their missions to the Moon and to Mars.
Ice is common in the solar system. Space is frigid, and many bodies are covered in ice. Could an in-situ IceBot be in the future?
Explore further